Stratification or Mixing Ventilation? The ultimate guide for HVAC planners
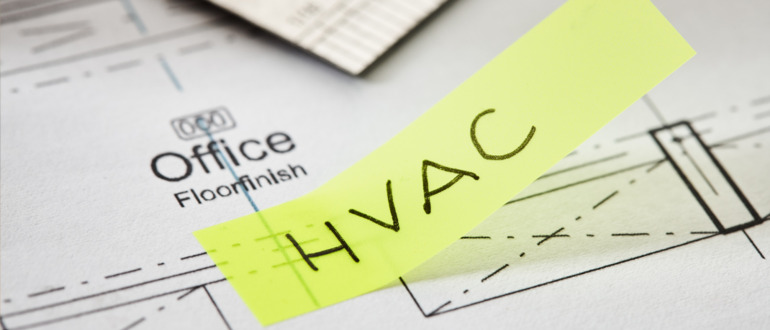
Stratification or Mixing Ventilation? The ultimate guide for HVAC planners
The selection of ventilation and air conditioning systems for production halls with extensive heating loads has always been a challenging part of planning and design.
Mixing ventilation
Figure 1: Mixing ventilation with decentralised roof ventilation units
Stratification ventilation
Figure 2: Stratification ventilation with decentralised roof ventilation units
Figure 3: Functional diagram for stratification ventilation
Calculation
Determination of the thermal air flows in accordance with VDI 3802 is done with semi-empirical equations, which are based on the boundary layer and turbulence hypotheses of Prandtl along with Reichardt’s open jet theory. They revert back in part to studies that started in the 1930’s. The thermal volume flow over one machine and thus the size of the subsequent supply air volume flow depends largely on its geometry and the surface temperature. Calculations for the horizontal and vertical areas are carried out separately.
The two proportionalities below shall apply for the horizontal machine areas, depending on the released heat Q and height z over the areas (Figure 4):
with Gr representing the Grasshof number and b the width of the vertical areas. It is assumed that the thermal portion of the vertical areas is completely induced into that of the horizontal areas. Based on experience, the horizontal areas provide the amount of air used for calculation.
One advantage of this air conduction concept compared to the conventional method is evident in a comparison of the equations]. In the stratification ventilation, the required supply air volume flow is proportionate to the third root of the released heat, i.e. clearly smaller than with direct proportionality as in. One can therefore arrive at smaller system sizes when using this air conduction concept.
Figure 4: Thermal upcurrent over one heat source
Application criteria
1. Required hall height
The basic thought process behind this air conduction method assumes a space above the stratified flow of the work area into which the loaded thermal upcurrent can first arrive. This means that a hall of suitable height is needed in order for the concept to work. But what is a suitable height?
One needs to be aware that the upper layer represents an area of mixed currents. If we assume the hall height is set up to be the same as the height of the supply air layer, a mixed current will result in this area. The laws under thus lose their validity and we are back to case. The height must be such that the impulse of the thermal upcurrent can be reduced during recirculation to the extent that no mixing with the lower layer occurs. Experience has shown that this requirement can be met if the hall height is set at
H = 3 x Layer height of the work area
For an area with a supply air layer of at least 2.0 and up to the recommended 2.5 m according to VDI 3802, this means a required hall height of 6.0 m to 7.5 m as a prerequisite for using this concept.
The semi-empirical equations are not suitable for consideration of boundaries when determining minimum hall height, since they do not reflect the actual physical correlation. That is accomplished by the Navier-Stokes equations, which, however, do not have a consistent solution for this application. The above-mentioned benchmark therefore serves as a useful guide when laying out a system.
2. Very large thermal air flows
As already mentioned, thermal air flows occur mainly due to the excess temperature of horizontal machine surfaces. If these values are very high, the following items must be checked:
- whether a portion of the horizontal surfaces can be located above and thus outside of the supply air layer by means of appropriately selecting the layer height,
- whether by attaching circumferential flanges around the surfaces in question up to the specified layer height, this amount of air can be taken out of the air volume equation (Figure 5),
Figure 5: Flange to reduce thermal air flow
- whether the required number of supply air outlets in the hall area can be arranged so that precisely the same amount of supply air can be brought in to match the local thermal volume flow from the machines. When very large volumes of supply air are required, it may actually become impossible to accommodate the required quantity on site.
3. Very small thermal air flows
Two situations must be observed if thermal air flows are becoming increasingly smaller,
- The supply air layer drops below the recommended range of 2.0 to 2.5 m in height. The transition from the stratified flow to the source ventilation is obtained. This means that people in the working area are breathing air from the more heavily loaded upper layer and the clean supply air layer is not effective for using this air conduction concept . Increasing the supply air flow to beyond merely replacing the thermal upcurrent will indeed result in lifting the height of the supply air layer, but will not lead to stable, static conditions. The excess supply air does not remain effective over the long term due to the equalization of temperature.
- The surface area of the zone theoretically formed around a production unit is considerably larger in proportion to the unit dimensions. At the edges of the calculated supply air layer the thermal upcurrent of the production unit will be of no influence so that interactions with the environment, i.e. temperature adjustment, will occur. This leads to a situation where a stable supply air layer is no longer possible and source ventilation is again set up. An adapted solution might only be found using a different method of air conduction, such as mixing ventilation.
4. Consideration of the instability of the thermal air flows
From a fluid dynamic point of view, thermal air flows are considered unstable, i.e. they are easily disrupted by crosscurrents. Studies have shown that crosscurrents with speeds of less than 0.1 m/s are sufficient to cause this disruption under weak thermal conditions. Particular attention must be paid to the following items to avoid this situation:
- The air volume balance of the individual regions of a hall must be adjusted. The same applies to neighbouring aisles of the hall, which are connected to each other by openings. Large hallway doors must be provided with air curtains to prevent crosscurrents due to the entry of cold air.
- The possible influence of a hall’s enclosing surfaces must be mathematically evaluated. This mathematical calculation is required in any case when monitoring the polluting and cleaning flow processes of a hall and includes a detailed consideration of the influence of the
a) Walls: If the walls have a lower temperature than the room temperature, a drop in cold air will occur. This perception is not new. This phenomenon has already been remedied for a long time using heating devices on poorly insulated walls, such as large window areas. The cold air flows that arise in this case can take on considerable proportions. Thus a wall that is 40 m long and 7 m high with a low temperature of 10 K compared to room temperature supplies a cold air flow of about 4300 m³/h. This can easily cause a disruption of the thermal if the above-mentioned measure is not implemented.
b) Ceilings, in particular shed roofs: For applications in which the transmission heat loss of the hall roof becomes greater than the heat gains from the machinery, the use of stratified flow is not recommended due to the fall in cold air that occurs. The reaction of shed roofs during times of low outdoor temperatures must be checked in particular to ensure that the selected air conduction concept can maintain its function throughout the year. To get an idea of the extent of the cold air flows which can develop, we consider a typical, steep shed roof section that is 20 m long and 2 m high and has a low temperature of 10 K compared to room temperature. A cold air flow of slightly over 500 m³/h is produced under these conditions. Taking an average hall length of 40 m with eight shed rows, a cold air flow of 4000 m³/h results, which, due to its opposite direction, sustainably disrupts thermal upcurrents, in particular weak ones. Depending on the strength of the flow, use of the stratification ventilation can be called into question.
- The driving force behind the stratified flow is the temperature difference of the machine surfaces compared to the room air. This effect occurs for basically every difference, even a very slight one. The tendency for thermal upcurrent to become unstable increases, however, with increasingly smaller temperature differences. Naturally, a limit to the practicality of stratified flow under these conditions also depends on the respective ancillary conditions and cannot be specified in general. In this case as well, as in some of the aforementioned items, the skill and sure instinct of the project leaders is required to decide when one or the other air conduction system should be used more efficiently.
5. Mutual dependency of several regions of a hall
To calculate the stratified flow, the hall must be divided into several regions depending on the type and occupancy of the production plants. The aim is to determine the required air volume in each case and thus the number of required air outlets for this area. The ancillary conditions of the supply air layer at the separating surfaces of bordering regions must be the same for purposes of continuity. Thus, it follows:
- that all regions of a hall must be laid out at the same layer height. Differing layer heights would balance out and result in a different height than the one calculated.
- that only regions of the same air conduction can be arranged next to each other. Stratification ventilation regions and mixing ventilation regions can therefore not exist next to each other, unless special measures have been taken.
Requirements for the ventilation of a production hall can be such that the optimum solution requires the application of more than just one air conduction principle. How can different air conduction methods be implemented in regions that are side by side without mutually influencing each other? Good results have been obtained in practical applications where areas are separated by plastic curtains. These curtains are put up from the ceiling to the supply air layer. Of course the neighbouring regions will not have all of the conditions of the particular air conduction principles as described in the definitions, but this will not cloud the overall results. This measure cannot always be applied. Requirements pertaining to internal logistics must be considered, in particular, just as the adjusted air volume balance between these two regions must be taken into account.
6. “Requirements” for pollutants
When using stratification ventilation, it is assumed that the pollutants are conveyed into the upper hall area with the thermal air flows. This process involves certain characteristics and requirements, which the pollutants must have and meet for the process to proceed effectively. Among these are:
- that the density of the pollutants is less than or equal to the density of the air. Considerably higher density levels result in more intense flushing in the supply air layer, both in the case of the thermal upcurrent and the upper, polluted layer.
- that the pollutants at the machine are released without impulse so that they do not migrate outside the area of the thermal upcurrent.
ensuring that there are no pollution sources outside the area of the thermal upcurrents.
Compliance with the above-mentioned provisions ensures that there will be no unintentional increase in concentration of pollutants in the supply air layer. This must be avoided at all costs, since the speed of the supply air is by its very nature so slow that virtually no induction occurs and therefore no mixing is possible. If compliance with these items is not possible, use of an alternative air conduction principle must be taken into consideration.
In addition, the provisions mentioned in the section “Consideration of the instability of thermal air flows” must be complied with. In so doing, the following items must be observed in particular:
- that the supply air velocity does not exceed the required 0.5 m/s at the air outlet, in accordance with VDI 3802, to avoid crosscurrents. If this cannot be complied with for air outlets arranged in the supply air layer, the situation can be remedied by placing them at about the 3 m level. Greater supply air velocities are first reduced here, after which the supply air flow sinks to the supply air layer of the work area due to its low temperature. But still applicable here: No pain no gain; on one hand, the supply air flows through a portion of the loaded upper layer, while on the other hand its low temperature must not be too high, so that the supply air flow does not accelerate too much and thereby disrupt the thermal as a crosscurrent.
- that the thermal upcurrent exhibits sufficient impulse upward, so that the pollutants can also be reliably conveyed into the upper hall area. In principle, as suspected during the initial view, the instability of the thermal upcurrent and therefore also the flushing out of pollutants decreases with increasing machine surface temperature.
Summary
The mathematical algorithm for stratification ventilation from VDI 3802 provides the project leader with a very efficient tool for planning the ventilation of a hall. It cannot be used blindly for every application, however. The most basic requirement is the existence of conditions that lead to the formation of two air layers with different densities. This can be brought about by the opposites cold – warm, as well as dry – moist. Procedures in which pollutants are released without heat yield cannot be handled in this way, for example.
The supply air layer height should not substantially deviate from the recommended values. As can be seen in light of correlation, a doubling of the height leads to a tripling of the supply air flow, i.e. extreme layer heights cannot be used meaningfully. This air conduction principle is an effective expansion of existing methods, during which particular attention must be paid to the requirements and limits.
If the article meet your expectations, please share!
Nomenclature